The evolution of denim and jeans in the US
(1700s - 1900s)
During the American Revolution (1765-91) the indigo dye was that valuable that indigo cakes were used as currency.
Indigo dye was also used for the blue colour in the first American flag, and George Washington directed that uniforms be dyed with Indigo.
Indigo cakes
First American flag
The word ‘denim’ was first cited in the US in 1789 when a Rhode Island newspaper reported that George Washington encountered ‘denim’ production on his recent tour of America’s largest cotton mill in Beverley, Massachusetts, where the mill was powered by horses.
Soon after in 1792 a book titled “The Weaver’s Draft Book and Clothier’s Assistant” published technical sketches of the weaving methods for a variety of different denims.
Subsequently, ever since Eli Whitney invented the Cotton Gin in 1794, which effectively did the work of 50 people in a day (separating cotton seeds from the fibre), the US cotton industry soared and both men and women wore denim in the US starting from the early 1800s.—the early adopters taking great pains to repair their denim garments and wear them for many years.
The FIT museum in New York exhibited a woman’s denim jacket circa 1850 – hand stitched, with gathered sleeves and shaped for a corseted figure;
also a pair of men’s jeans circa 1840.
Both items are dyed with natural indigo.
The museum at FIT, “Denim: Fashion’s Frontier.” Woman’s jacket. Blue Denim. Circa 1850, USA.
The museum at FIT, “Denim: Fashion’s Frontier.” Woman’s jacket. Blue Denim. Circa 1850, USA.
The museum at FIT, “Denim: Fashion’s Frontier.” Men’s jeans. Blue Denim. Circa 1840, USA.
The museum at FIT, “Denim: Fashion’s Frontier.” Men’s jeans. Blue Denim. Circa 1840, USA.
__________
So the real history of denim in America dates back to the 1840s, when the durability of this warp-faced textile becomes a proven choice for workwear clothing. The demand was for pants and overalls mostly, what with the industrial boom in the US at the time.
During the California gold rush of 1848-1855, the sight of a prospector dressed in his denim work clothing- field jacket, and hip waders (or waist overalls) is a common one.
Slave owners also bought denim for their enslaved workers (sharecroppers), partly because the material was sturdy, but also because it helped contrast them against the linen suits and lace parasols of plantation families.
Prospectors dressed in their denim work clothing - field jacket, and hip waders (waist overalls). 1850s
Gold Rush prospectors at the La Grange Mine, California. 1850s
The black sharecroppers of the American South through old photographs, 1939-41
The black sharecroppers of the American South through old photographs, circa 1900
__________
As touched on above, denim garments from the 1850s were made with yarn spun on Ring Frames- Ring Frames being the next-generation industrial equivalent of the Spinning Wheel or Spinning Jenny, based on the same method of rolling the fibres into shape using a system of spindles, for both warp and weft.
The spun yarn was then dyed through a process of hank or skein dyeing - or rope-dyeing from 1915. This involves dipping hanks (or skeins), or ropes, of yarn- effectively bundles of yarn- into successive dye vats followed by a period of ‘skying’ (oxidation) after each dip, and results in a depth and richness to the hue that is still sought after (considered a luxury) today.
The dyed yarn was then woven into fabric on shuttle looms - both the hand and early power operated ones - where the weft thread (crosswise) is interlaced with the warp thread via a thread carrier which was a wooden shuttle travelling back and forth across the warp continuously, and with a single continuous thread- battened down at each end without a break in the thread during the process. Creating a clean woven edge to the fabric known as a self-edge or ‘selvedge’ (or ‘selvage’).
The above three processes - namely ring-spinning on a Ring Frame, rope-dyeing, and shuttle-loom weaving, remained the industry-adopted methods for spinning, dyeing, and weaving right through to the end of the 1970s.
Then in the ‘80s, in order to address the sudden surge in the demand for denim (globally), it was around the mid-’80s that we see the industry-wide switch to the several times faster and cheaper open-end (rotary) spinning, and slasher or sheet dyeing as opposed to rope-dyeing, and the larger format shuttle-less, Projectile looms (as opposed to Shuttle looms) for the weaving.
And this was the key - the change in the spinning especially- where it was now a different kind of denim that was being produced, with a change in its core, due to the change in the spinning, creating a less compact but also a different kind of yarn, with a different hand - the consequences of which weren’t quite understood or forseen by the consumer or even the industry at the time, and still remains a question mark or mystery to many, although the frustrations - and the reverence (for vintage) - is very much there.
__________
Going back to the 1800s, the next major breakthrough in denim and jeans was the invention (and patenting) of the rivet in 1873, by Jacob W. Davis, a tailor from Reno, Nevada, and Levi Strauss, a fabric wholesaler based in San Francisco.
Strauss and Davis addressed the major problem for work wear garments of too easily ripping at the pocket seams, resolved by applying rivets to both the front and back pockets (though the back pocket rivets were eventually replaced with bar-tacs).
Levi Strauss (left), and Jacob W. Davis (right)
US Patent No. 139,121.
May 30, 1873
Levi’s Ad, circa 1890
Levi’s Ad, circa 1890
A pair of vintage Levi’s jeans, from circa 1890
A pair of vintage Levi’s jeans (with the single back pocket), circa 1890
Levi Strauss & Co., company headquarters building, Sacramento Street, Sanfrancisco. (circa 1910)
The Davis/Levis partnership and the rivet led to a meteoric surge in the demand for blue jeans as work wear in the Western states, in the US. This initially involved miners, railroad workers, and factory workers, but soon extended to the ranchers and cowboys out West.
Miners wearing Levi’s jeans outside Last Chance Mine, in Placer County, California. circa 1882
Farmers in jeans, circa 1900
Calgary cowboys in jeans, Alberta. 1883
Branding at Brown Ranch, Alberta. circa 1900.
Vintage jeans (Levi’s). circa 1920
Bar U Ranch cowboys, general round up, Southern Alberta. 1901
With the sky-rocketing in the demand for rivet-enforced jeans as work wear, again as touched on a little earlier there were a parallel developments in the manufacturing that aided and accelerated the growth and popularity of jeans further.
__________
Back to Indigo.
Indigo = “Blue Gold”
In 1878 the basic chemical structure of indigo was discovered and synthesised by the German chemist Adolf Von Baeyer (for which he was awarded the Nobel Prize in Chemistry in 1905)- and synthetic indigo was synthesised to have exactly the same chemical composition and properties as natural indigo.
Indigo is a unique dye in that it doesn’t form a chemical bond with the fabric as in other dyes, just a physical bond and hence it doesn’t penetrate the fabric in the same way but rests in layers on the surface, which with prolongued wear erodes away- hence the sought after fade.
Indigo also has a high pH of anything between 10 and 12 which it is said acts as a preserving agent- and this may go some way to explaining why jeans do not need to be washed as often. (Also helps to explain why on testing a worn pair of jeans after 2 weeks, and unwashed after 3 months, the extent of the layer of oil, grease and dirt is more or less unchanged.)
These characteristics may also account for why since its birth in ancient times in Asia- which went to great lengths to extract and then convert this dye from its plant form- and also in pre-medieval and medieval Europe (starting from Greece and Rome dating back to 300 b.c.)- indigo was sought after as a luxury item in spite of the levies, often referred to as “blue gold”.
It also continues to this very day to seduce successive generations.
Furthermore, indigo dyed jeans also have the peculiar characteristic of looking better dirty, unwashed, and non-pristine- with that worn-in, gritty look giving jeans their edge- which only further compounds and obviates the need for them to be washed, hence their value in workwear, and also in fashion.
By 1897 commercial chemistry giants BASF and HOECHST had their own version of synthetic indigo patented and in 1904 simplified the process of synthesising indigo even further, resulting in a more consistent and stronger dye, and less than a decade later the production of synthetic indigo had almost completely replaced naturally derived indigo on the world market.
Only India went on producing indigo from the plant until the 1st World War, and today Indigo Tinctoria is cultivated in small amounts in Brazil and El Salvador, while there is talk of some recommencement in the US, in South Carolina.
Natural indigo jeans are generally of a lighter blue than those dyed with synthetic indigo- and the colour saturation and colour purity of synthetic indigo today is far superior to that of natural indigo- and its production today easier, cheaper and also environmentally friendlier (ref. Thomas Stege Bojer, June 9, 2017 for Denimhunters*).
For those who are interested- both natural and synthetic indigo must be ‘reduced’ to their soluble form prior to dyeing the yarn, and the reducing agent (sodium hydrosulphite or sodium dithionite) gets converted to sulphite and sulphate in the process, and this needs to be neutralised or filtered as it’s toxic to marine life.
There is also a more traditional natural way to reduce indigo without the use of hydro-sulphites e.g. with bacteria – leaving a waste that is simply water and plant matter that can be used as fertilizer, and this method is sometimes used in Japan.
On a further point of toxicity, generally well-dyed indigo denim in recent years is produced with ‘safe’ to negligible amounts of aniline and other toxic substances that could otherwise be harmful when washed out of the jeans.
In the US there are strict regulations in place requiring US plants to purify waste water.
There is also new nano-cellulose technology that doesn’t ‘reduce’ the indigo into soluble form- it mixes the indigo with nano-cellulose-fibrils (wood pulp) and then deposits them onto the surface of the yarn, effectively gluing the colour in place- and one dip of this achieves a higher colour-fastness than 7-8 dips of the soluble method, and it doesn’t require water.
Rope dyeing
Then in 1915 Rope-dyeing was automated and established- a kind of next stage progression of hank or skein dyeing (the go-to method of dyeing denim since the 1500s).
It was based on similar principles of dipping bundles of yarn (now ropes) into successive dye baths, followed by skying (oxidation) after each dip. Only with the ropes you now got the bonus of a ‘ring-dye’ effect (varying degrees of penetration of the dye where the surface area of the ropes is more- or less- exposed).
Rope-dyeing, since replaced (in the 1980s) by the 7-9 times faster and cheaper ‘slasher’ or ‘sheet’ dyeing, is now also sought after for its quirky, dynamic and a kind of multi-dimensional finished look with respect to the ‘ring dye’ that it gives. It also introduces a greater sense of depth to the weave, as well as a deeper, richer hue and better fade characteristics (than with the modern day slasher or sheet dyeing method).
Hank dyeing, an example of
An indigo dyed hank of yarn
Skein dyeing (6 skeins = 1 hank)
Skeins of yarn dyed indigo with different levels of saturation (no’s of dips)
An industrial rope-dyeing plant. circa 1980
Rope-dyed yarn
Other than in the spinning (ring spinning) the key to creating beautiful denim today is in the dyeing: rope-dyeing.
The modern day “slasher” or “sheet” dyeing, which replaced rope-dyeing industry-wide in the 1980s, involves beaming the yarn onto large sheets, then dipping the sheets into successive dye baths.
This process creates a more basic, uniform, even look to the dyed yarn (without the “ring dye'“ effect that you achieve with the ropes). It also lacks that genuine depth of hue and richness of caste that you get with the ropes, and crucially there is also - and this is again the key- a less characterful fade propensity to the dyed fabric.
Traditional rope-dyeing was the go-to method of dyeing denim throughout the industry, globally right up to the mid 1980s, and - to repeat - the modern day slasher or sheet dyeing is what virtually the whole industry switched to, globally, in the 1980s- other than a handful of premium denim mills in Japan, and Italy.
A modern day indigo slasher (or sheet) dyeing plant
__________
Ring spinning
Ring-Spinning: The invention of the Ring Frame, as credited to John Thorpe in Rhode Island in 1829 but being actively taken up in the US from the 1850s, vastly increased the speed and capacity for spinning yarn as compared to its predecessors the Throstle Frame and Arkwright’s Water Frame (of 1765).
- in turn based on the same principle of spinning thread using rotating spindles, as is the Spinning Wheel and the Spinning Jenny.
After the American Civil War (of 1861-65) mill building started in the South as a way of providing employment, and these mills used Ring-Spinning machines (Ring Frames) to produce their twill fabrics such as denim.
In 1871 Jacob Sawyer vastly improved the spindle for the Ring Frame- increasing its efficiency further.
And it’s in the spinning, this is the real key to creating beautiful denim.
The strongest, most beautiful denim is dual-ring-spun (aka “ring x ring” denim), where both the warp and weft yarns are ring-spun.
Vis a vis the mass produced denim you get today which is either
(a) open end (rotary spun);
or (b) ring-spun where just the weft yarn is ring-spun and the warp is open end.
Ring spinning - so to speak - is how denim yarn was spun from the 1500s right through to the end of the 1970s, and open-end (or ‘rotor’) spinning is how the vast majority of denim yarn has been spun since, from the mid-1980s.
Open-end spinning can deliver yarn 7-9 times faster than ring-spinning.
In ring spinning the fibres are rolled into shape by being wound around a rotating spindle, whereas in open end (rotary) spinning the fibres are twisted and effectively pressed into shape through a centrifugal action, by air currents.
Ring spinning produces a stronger, more compact yarn, and also a softer and silkier hand- in addition to the higher durability and tensile strength.
Ring spinning also introduces ‘slubs’- natural imperfections created through the process, that in denim give it what is deemed true character and beauty and- keenly- that certain ‘authentic denim’ quality in terms of appearance.
Dual-ring-spun denim can be sourced today but via only a handful of Japanese mills, and one or two in Italy.
Ring-Spinning: the Spinning Wheel, an early example of
Ring-Spinning: Richard Arkwright’s Water Frame, as first used in 1765.
Patented in 1769
Originally powered by waterwheels (and horses).
Ring-Spinning: the Ring-Frame at Kurabo Mills, Japan. Circa 1915
Ring-Spinning: 84 spindles, small-type modern Ring-Frame
Open End Spinning: A modern day rotor open-end spinning machine
Open End Spinning: Titan, TQF 368, Rotor Open End Spinning Machine
__________
Weaving – Shuttle looms versus the modern day Projectile looms
As to differences in the weaving, between then and now, which is where some denim heads take particular pride, this isn’t truthfully the same sine-qua-non for exquisite looking, core-integrity denim as is the spinning or the dyeing, but it’s a key signal for some as to the probable integrity of its make up, namely that denim elected to be woven on a shuttle loom today- shuttle looms being the more traditional, more expensive, slower and less productive weaving machines- is most likely also to be dual-ring-spun and rope dyed.
That said, due to the current day fascination with ‘selvedge’- where it’s become something somewhat heralded and prized of itself (initially due to its associations) - this is not quite so true anymore, with some manufacturers using shuttle looms to producing selvedge denim, which at its core is open-end and sheet-dyed.
__________
The flying shuttle loom was invented and patented by John Kay in 1733, which increased the efficiency of weaving several times over from the hand loom.
In 1894 the first fully automated shuttle loom was introduced, by the Draper Corporation, in the US.
[With John Kay’s loom, as the shuttle travelled weft-wise across the warp ran out of yarn, as it ran out of thread the machine would stop and the shuttle would have to be manually refilled or replaced.]
So the invention of the fully automated shuttle loom by the Draper Corporation in 1894 significantly improved the capacity and cost for weaving denim.
The Draper’s automatic loom, known as “The Northrop”, became a huge success in the US and by 1914 Northrops made up 40% of looms in American mills.
Picanol from Belgium and Toyoda from Japan (the precursor of today’s Toyota Motor Corporation) also made competing, fully automated shuttle looms, but it was the Draper that was most recognised and adopted in the US.
While weaving on a shuttle loom is slow (5-6 times slower) compared to the larger format shuttle-less Projectile looms of today, the vast majority of US denim right up to the end of the 1970s was woven on Draper shuttle looms. It was only in 1985 that Cone Mills, the then main denim supplier to Levis, Wrangler and Lee, replaced all of its Draper X3 shuttle looms with the larger format Swiss Sulzer (Projectile) looms.
Shuttle loom design is today loved for its aesthetics- the lower tension on the yarn, due to its lower speed, as compared to the super-speed modern day Projectile looms- weaves denim in such a way that it subsequently fades more beautifully, and the loom also tolerates more slubs (those prized characterful imperfections within the ring-spun yarn that it would normally fed with).
The sheer weight and momentum of the 40cm long shuttle crossing the 30” wide shed of warp threads (of the weaving frame) back and forth in a zig-zag at three times per second, against the clunky, heavy machinery of the loom, then brings on its own intern or shudder, known as ‘loom chatter’- introducing its own unique rhythm, mood swings or you could say fingerprint- or ‘soul’- into the woven fabric.
And whereas this characteristic in other fabrics would be passed off as an error, as imperfections, in denim it would only add to the beauty (and the sense of depth and dimension), at the same time impossible to replicate.
The single- unbroken- weft thread that is being interlaced in a shuttle loom, back and forth, through the warp yarn, battened down at either end, gives a clean woven edge to the fabric known as a ‘self-edge’, or ‘selvedge’ or ‘selvage’.
And yes, selvedge has become synonymous with denim woven on shuttle looms vis a vis the vulnerable raw edge that’s created on the larger format Projectile looms of today, where weft the thread is cut and then re-inserted each time on its crosswise journey through the warp.
So, to repeat, virtually all denim globally right up to the end of the 1970s was woven on shuttle looms and self-edged (which also accounts for the then popularity of cuffed denim).
Then, ever since the 1980s, the speed of weaving from around 140 to 160 picks per minute on shuttle looms was multiplied several times over to around 400-600 picks per minute on the newer larger format Projectile (shuttle-less) looms, and the width of the weaving frame (and hence of the fabric) was also doubled from 30” to 60” or wider still- now that no longer was there a heavy shuttle that had to be propelled back and forth across the width of the frame.
It is also true however that around the same time, from the 1980s onwards select Japanese mills came forward and experimented with techniques based on the old school method (using ring-spinning, and rope-dyeing - which were the real key - and then also shuttle-loom weaving, which is for some “denim heads” the final part of the true equation)- and they began to push the limits of what denim is, beyond that of the heritage.
They created in the ‘90s and through the 2000s (and still are creating, to the present day) heavier, more slubby, softer, silkier, more exquisite, more beautiful and more hard-wearing denim than ever before, albeit at price points that would exclude all but the higher bracket of the premium denim heirarchy.
The myth about Japan
It is also true that Japan scooped up many of the old American Draper shuttle looms when the American mills re-automated to the (shuttle-less) Projectile looms. But it is also a bit of a myth that Japan’s success in this area is down to their having purchased the old Draper looms.
- The vast majority of shuttle looms in Japan are Toyoda (the precursor of the Toyota Motor Corporation).
There is a Draper on display at the Evisu store in Tokyo, owned by Hidehiko Yamane, the man who created the myth-
possibly to romanticise Japanese denim heritage with a bit of Americana, in order to help sell jeans.
The Vidalia Mills, Louisiana
Romanticism around selvedge continues to grow in the US.
46 of the 51 Cone Mill’s White Oak Plant Draper X3 shuttle looms having been bought up in 2018 (after the closure of White Oak in 2017) by the Vidalia Mills in Louisiana, and the remaining 4 by the Huston Textile Co in Sacramento, California.
Vidalia even went to the extent of importing in White Oak’s (Cone Mills’) wooden floors to replicate the shudder and resulting ‘loom chatter’ – although weavers discovered that placing rubber footings under the looms preserved their quirky shudders and shakes just fine.
The first of the Cone Mills’ Draper X3 Shuttle Looms re-housed at the Vidalia Mills in Louisiana in 2018
A Sakamoto Shuttle Loom, Japan. circa 2015
Weave room at Cone Mills’ White Oak plant in Greensboro, N.C., USA. - housing its 56 Draper X3 shuttle looms - prior to its closure in 2017
Weave room at Cone Mills Mexico plant, featuring the modern day larger format shuttle-less Sulzer Projectile Looms. circa 2015
__________
__________
site edited by Sheel Khemka BA (OXON)
© 2022.
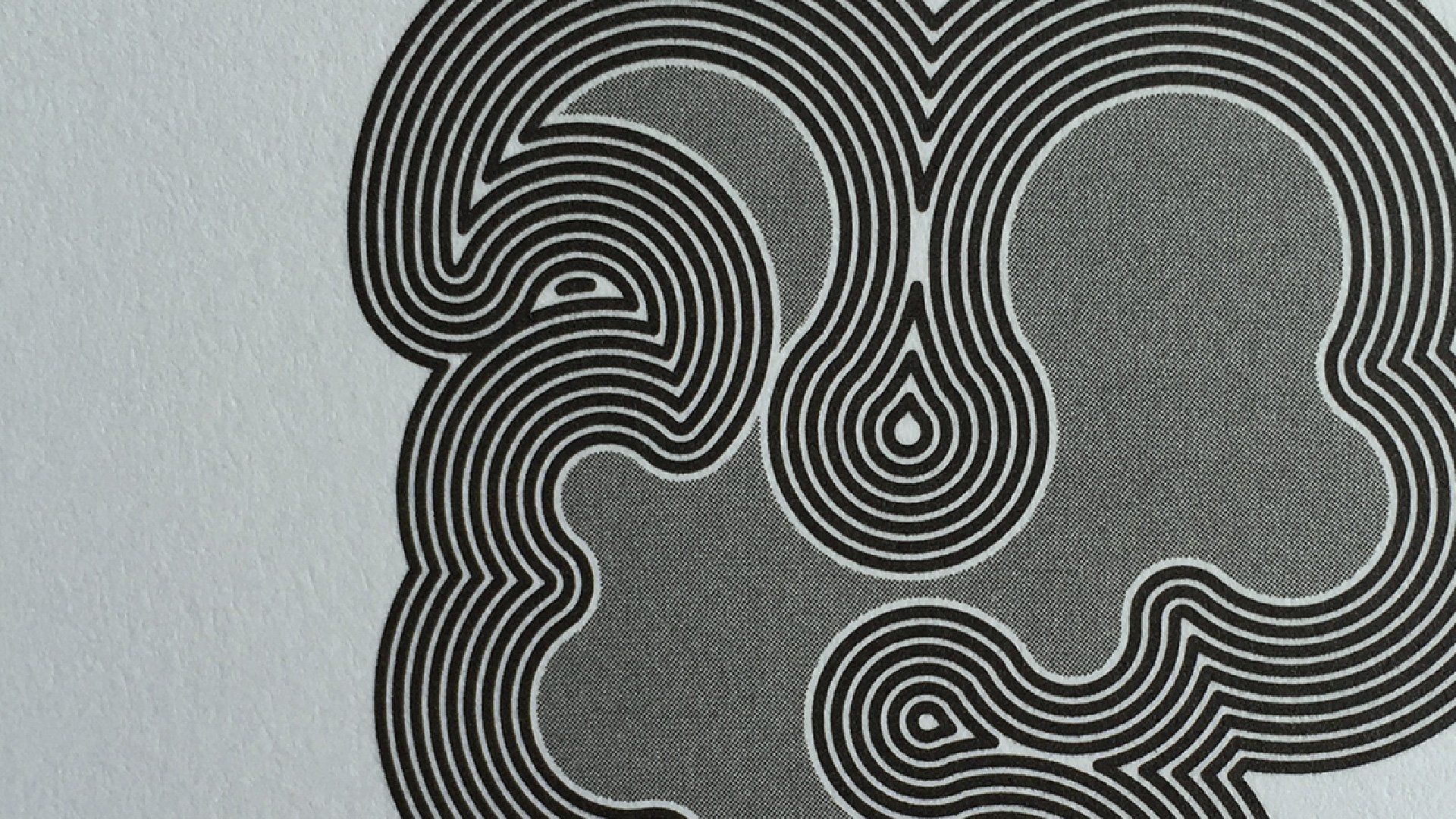
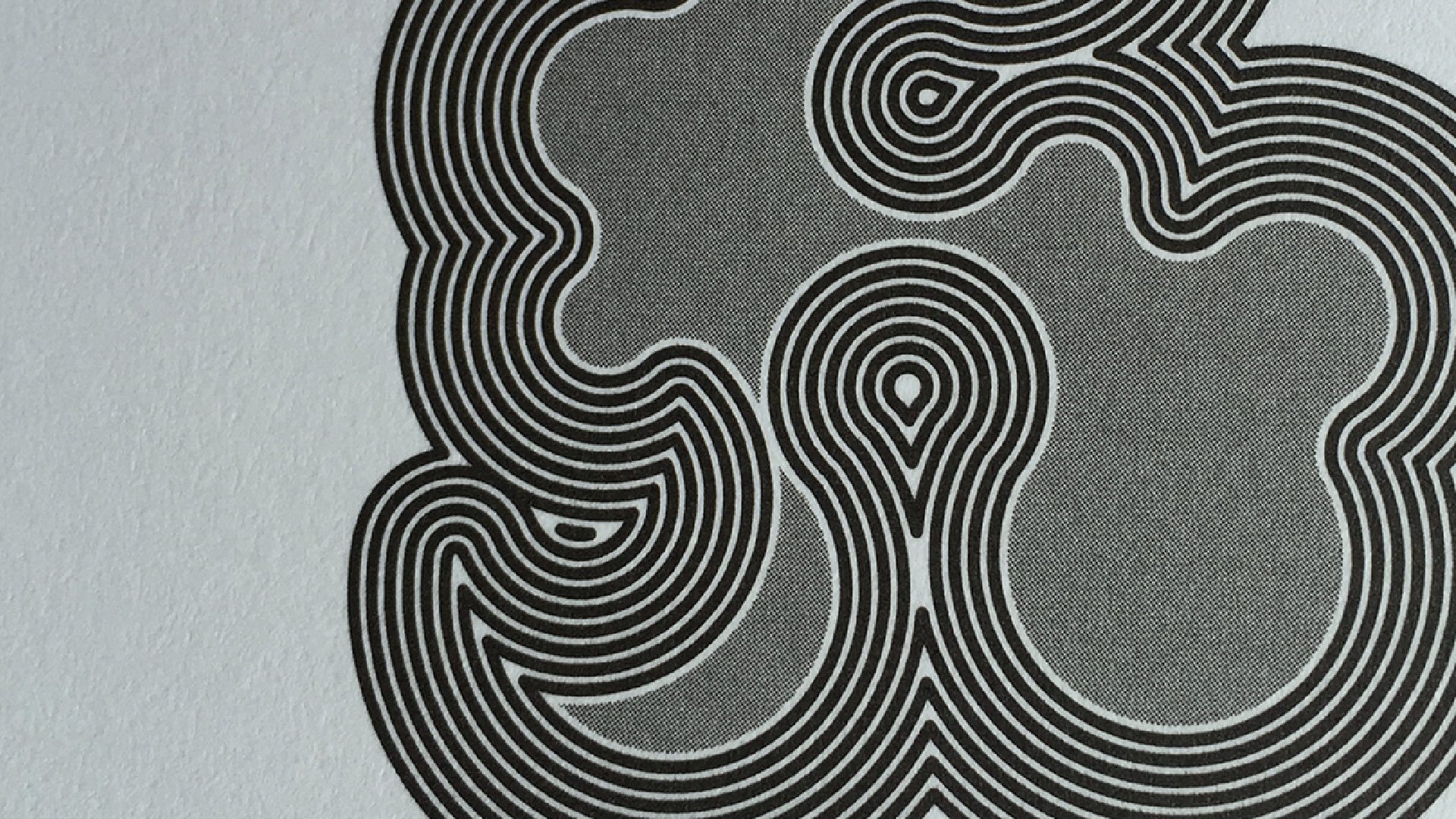
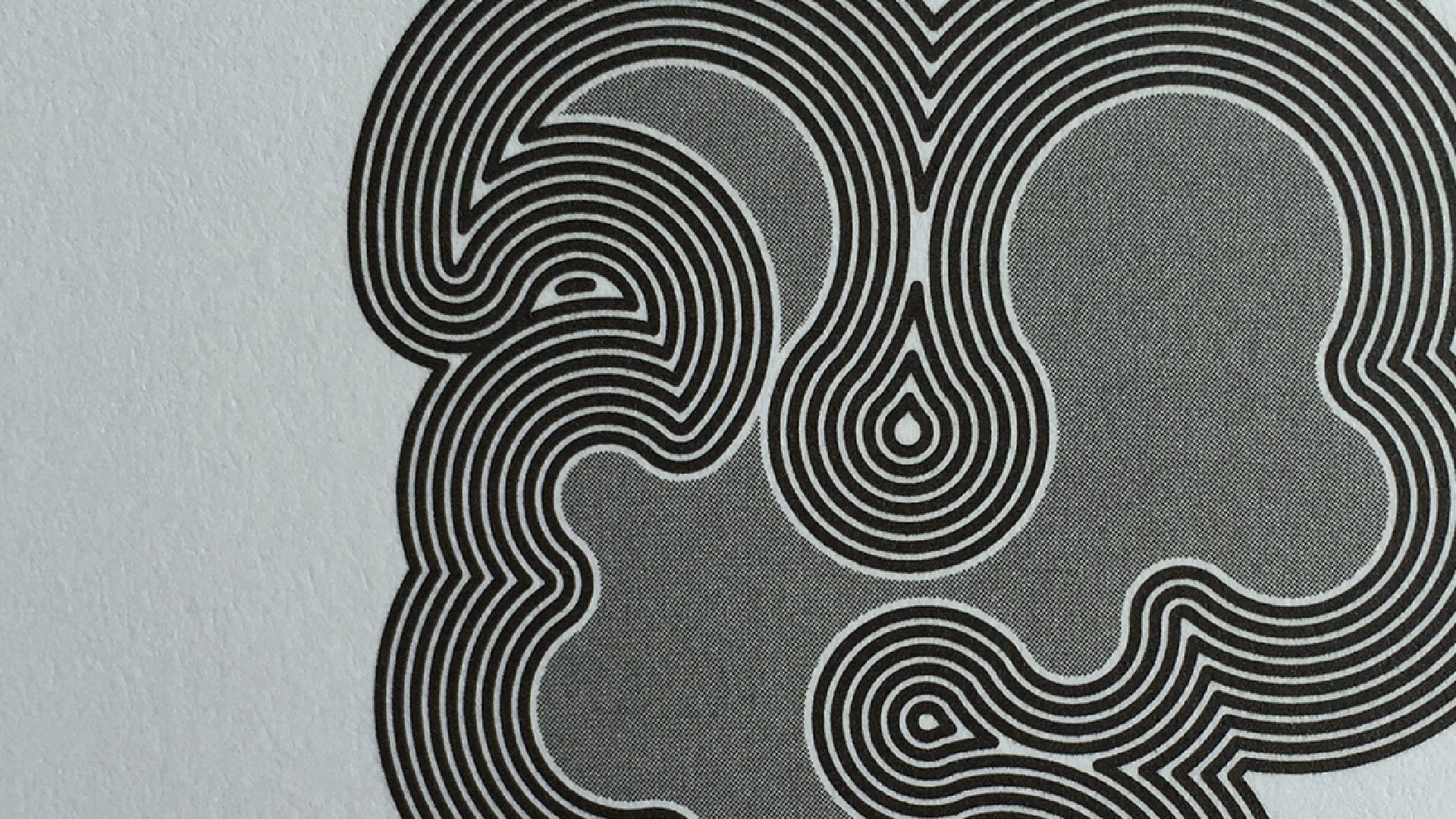
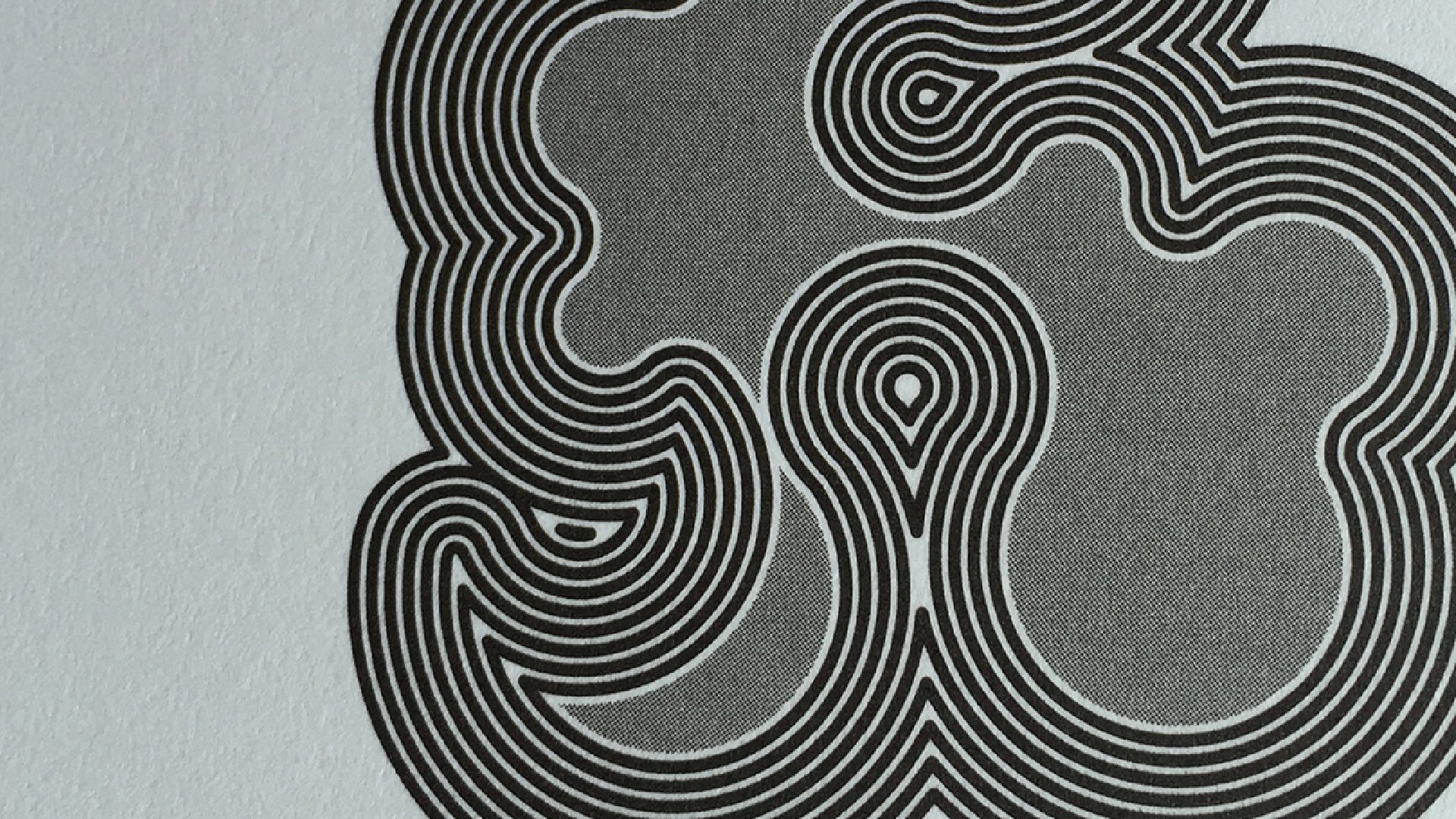